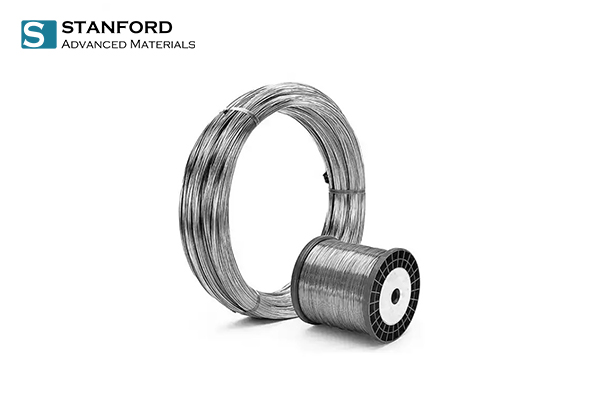
The metal Titanium has many unique physical and chemical properties. It is nearly as corrosion-resistant as platinum. It has also excellent acid, salt solutions, and even chlorine gas and temperature resistance. It may be 60% heavier than aluminum, but 100% stronger. It is 45% lighter than steel but equally strong. In addition, the element Titanium is also abundant in nature. Therefore, for the auto industry, the metal Titanium is an incomparably promising material. According to the data from the German Fraunhofer Institute for Machine Tools and Forming Technology IWU, automotive components made from titanium would be 40% lighter than those made from other metals. However, this white silver lustrous metal remains in the shadows of steel, Chrome, Nickel, and aluminum when it comes to manufacturing. Parts such as manifolds, exhaust pipes, catalytic converters, and mufflers are primarily manufactured from high-alloy stainless steel. The reason for this is that there isn’t a method of cost-effectively forming technologies for titanium.
Efficient metal forming processes such as deep drawing or hydroforming can only be used in a very limited way. Titanium tends to adhere to the forming tools, which can lead to component cracking and severe damage to the surface. This leads to major damage which can cause components to fail in the worst case. This effect is amplified by the extremely high temperatures of up to 800 °C, at which titanium has to be formed.
Forming titanium at room temperature leads to severe cold work hardening of the processed pipe. In order to prevent cracking, the metal requires frequent treatment by means of recrystallization processes. This leads to extremely complex multi-stage forming processes which are not economically viable in large-volume production of exhaust systems. This microstructural change can be avoided at extremely high temperatures.
The most recent news is that the technical obstacle mentioned above is expected to be broken through by the cooperation between the above German institute and Thin Films IST. They have developed a new technology for hydroforming Titanium car exhaust systems at elevated temperatures.
This new method enables forming to be undertaken in a single process stage. The scientists have now developed a process and custom tool which can withstand temperatures of over 800 °C. The approximately 1.40 x 1.20 meter forming tool is manufactured from high-performance materials such as Nickel-base alloys which remain stable at temperatures over 800 °C without oxidizing. A special coating, just a few micrometers thick prevents titanium from adhering to the tool. Martin Weber, an expert for new tribological coatings at IST says: “At temperatures from approximately 500 °C, titanium exhibits a strong tendency to combine with oxygen and nitrogen from the surrounding atmosphere. For this reason, it is necessary to work with shielding gases at extremely high temperatures, such as argon, in order to prevent the oxidization of titanium. After extensive testing with various materials, we were able to develop the ideal coating for the special conditions encountered within the various temperature ranges”.
The researchers are going to present the initial results of the joint project at the EuroBlech trade fair in Hanover on October 23 and 27.