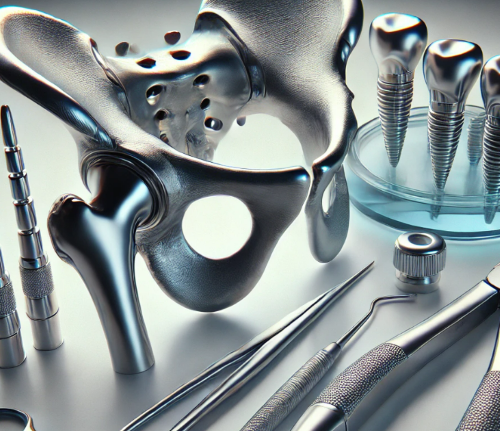
Introduction
Titanium has become a critical material in the medical device industry, offering an unparalleled combination of strength, lightness, and biocompatibility. These properties make it indispensable in the manufacture of implants, prosthetics, and surgical instruments. This article will talk about its unique characteristics, its applications in healthcare, and its future potential in advancing medical technology.
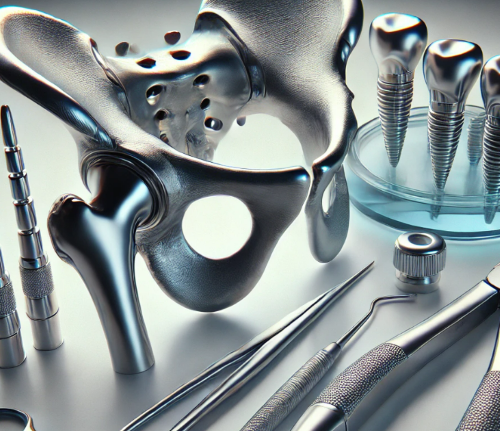
Unique Properties That Drive Its Use
Titanium’s high strength-to-weight ratio is one of the key reasons for its widespread use in medical devices. It is as strong as steel but much lighter, which is particularly important in applications where minimizing weight is crucial for patient comfort and mobility. For example, in orthopedic implants like hip and knee replacements, a lighter implant means less strain on the patient’s body, leading to quicker recovery times and improved long-term outcomes.
Related reading: 6 Major Uses of Titanium
Another critical property is its biocompatibility. Unlike many other metals, titanium does not provoke an immune response when used inside the human body. This biocompatibility is due to the formation of a stable oxide layer on its surface, which prevents corrosion and reduces the risk of inflammation or rejection by the body’s immune system. This makes it an ideal material for implants that need to be in close contact with bone or tissue.
In addition, this metal has a unique ability to bond with bone, a process known as osseointegration. This property ensures that implants made from this material remain securely anchored within the body, promoting long-term stability and functionality. This is particularly important for dental implants and orthopedic devices, where the implant needs to become a permanent part of the patient’s anatomy.
Moreover, titanium is non-magnetic, which is a crucial consideration for patients who may require magnetic resonance imaging (MRI) scans. Unlike other metals that can interfere with MRI procedures, this metal is compatible with these scans, allowing patients with implants to undergo imaging safely without risking damage to the implant or compromising the quality of the images.
Key Applications in Medical Devices
Orthopedic implants are one of the most common applications for titanium in the medical field. Hip and knee replacements, for example, rely on this metal for its strength, lightness, and ability to bond with bone. These implants need to be both durable and lightweight to provide patients with improved mobility and reduced pain. By using titanium, manufacturers can create implants that are not only strong and long-lasting but also comfortable for patients to use.
In dental medicine, titanium is the preferred material for dental implants. These implants are used to replace missing teeth and provide a stable base for artificial teeth. The metal’s ability to osseointegrate with the jawbone ensures that dental implants are securely anchored, providing long-lasting results and improving oral health. Patients with dental implants benefit from increased confidence, better chewing ability, and a more natural appearance.
Cardiovascular devices such as pacemakers and heart valve replacements also rely on titanium for their construction. The metal’s corrosion resistance is vital in these applications, as these devices must function reliably within the body’s circulatory system for extended periods. Additionally, the non-reactive nature of this metal minimizes the risk of the body rejecting these implants, making it a safer option for patients. The use of titanium in these devices has saved countless lives by providing reliable and long-lasting solutions to heart-related conditions.
Beyond implants, titanium is widely used in the manufacture of surgical instruments. Its strength and resistance to wear make it ideal for precision instruments that need to maintain their sharpness and accuracy over many uses. Additionally, the lightweight nature of titanium instruments reduces the strain on surgeons during long procedures, improving their control and dexterity. This not only benefits the surgeons but also enhances patient outcomes by allowing for more precise and effective surgical interventions.
The Future of Titanium in Healthcare
As medical technology continues to advance, the demand for titanium in the healthcare sector is expected to grow. One area of particular interest is the development of advanced titanium alloys that offer even greater strength, lighter weight, and improved biocompatibility. These alloys could expand the range of applications for this metal in medical devices, potentially leading to new and innovative treatments for a variety of conditions.
Another promising avenue is the use of additive manufacturing, or 3D printing, to create customized titanium implants and devices. 3D printing allows for the production of complex geometries and patient-specific implants that are tailored to the individual’s anatomy. This technology has the potential to revolutionize the way implants are designed and manufactured, offering personalized solutions that improve patient outcomes. Custom implants could lead to better fitting devices, reducing complications and enhancing the overall effectiveness of the treatment.
Furthermore, as the global population ages and the prevalence of conditions such as osteoporosis and arthritis increases, the need for durable, reliable medical implants will only become more pressing. Titanium’s proven track record in medical applications makes it a likely candidate to meet this growing demand. The metal’s durability ensures that implants can withstand the wear and tear of daily life, providing patients with long-term relief and improved quality of life.
Conclusion
Titanium’s strength, lightness, biocompatibility, and resistance to corrosion have made it an essential material in the medical device industry. As technology advances and new applications emerge, its role in the medical field is set to expand, continuing to support the evolution of healthcare and the development of innovative medical solutions. For more information, please check Advanced Refractory Metals (ARM).