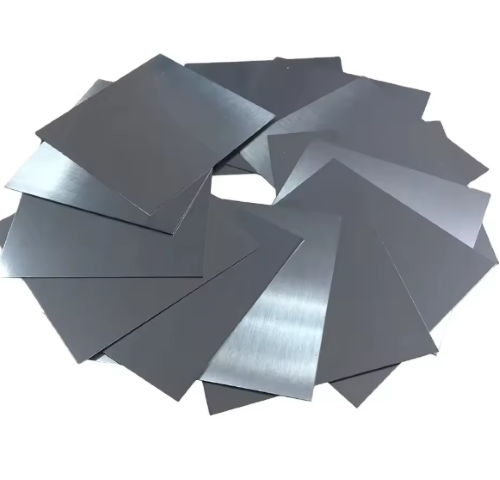
Introduction
Titanium alloys are used in many industries because of their high strength, low weight, and resistance to corrosion. These alloys are essential in aerospace, medical, and industrial applications. Here, we discuss six common types of commercial titanium alloys: Grade 1, Grade 2, Grade 5, Grade 7, Grade 9, and Grade 23. Each alloy has unique properties that make it suitable for specific uses.
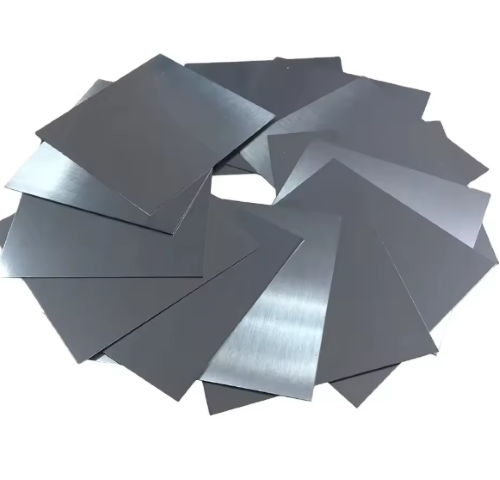
1. Grade 1 Titanium Alloy
Grade 1 titanium is the purest form of titanium. It contains at least 99.5% titanium. This alloy is known for its excellent corrosion resistance and high ductility. It is also very easy to form and weld. Grade 1 titanium is often used in applications where maximum corrosion resistance is essential. Examples include chemical processing plants, desalination plants, and marine environments. Its high ductility also makes it useful in medical devices and implants.
Related reading: Development & Wide Applications of Titanium Alloy
2. Grade 2 Titanium Alloy
Grade 2 titanium is also commercially pure but slightly stronger than Grade 1. It contains a small amount of oxygen, which increases its strength. Grade 2 titanium is known for its balance of strength and corrosion resistance. It is easy to weld and form, making it versatile. This alloy is widely used in industries such as aerospace, where it is used in airframe components and jet engines. It is also used in power generation, chemical processing, and medical equipment.
3. Grade 5 Titanium Alloy (Ti-6Al-4V)
Grade 5 titanium, also known as Ti-6Al-4V, is the most commonly used titanium alloy. It contains 6% aluminum and 4% vanadium. This alloy is known for its high strength, low weight, and excellent corrosion resistance. Grade 5 titanium is used in many high-performance applications. In the aerospace industry, it is used in jet engines, airframes, and spacecraft. It is also used in medical implants, such as hip and knee replacements, and in sports equipment.
4. Grade 7 Titanium Alloy
Grade 7 titanium is similar to Grade 2 but with added palladium. The palladium increases the alloy’s resistance to corrosion, especially in reducing and oxidizing environments. This makes Grade 7 titanium suitable for highly corrosive environments, such as chemical processing plants. It is also used in industries where superior corrosion resistance is required, like oil and gas exploration.
5. Grade 9 Titanium Alloy (Ti-3Al-2.5V)
Grade 9 titanium, or Ti-3Al-2.5V, contains 3% aluminum and 2.5% vanadium. This alloy has a good balance of strength and formability. It is stronger than Grade 2 but more formable than Grade 5. Grade 9 titanium is often used in aerospace applications, particularly in hydraulic tubing and aircraft structures. It is also popular in the sports equipment industry, especially for bicycle frames and golf clubs, due to its combination of strength, lightweight, and corrosion resistance.
6. Grade 23 Titanium Alloy (Ti-6Al-4V ELI)
Grade 23 titanium, also known as Ti-6Al-4V ELI (Extra Low Interstitial), is a variant of Grade 5 titanium. It has lower levels of oxygen, nitrogen, and iron. These lower levels enhance its fracture toughness and ductility. Grade 23 titanium is primarily used in the medical field for surgical implants and devices. Its superior biocompatibility makes it ideal for use in the human body. It is also used in aerospace applications where high strength and low weight are critical.
Conclusion
Titanium alloys offer diverse types and are suitable for various commercial applications.
Grade 1 and Grade 2 titanium provide excellent corrosion resistance and are easy to form and weld. Grade 5, the most widely used alloy, combines high strength with lightweight. Grade 7 offers superior corrosion resistance with the addition of palladium. Grade 9 strikes a balance between strength and formability. Finally, Grade 23 is highly biocompatible, making it ideal for medical implants.
Understanding the differences between these alloys helps industries choose the right material for their specific needs. Each grade of titanium alloy has unique characteristics that provide solutions to engineering challenges in diverse fields. For more Niobium products, please check Advanced Refractory Metals (ARM).