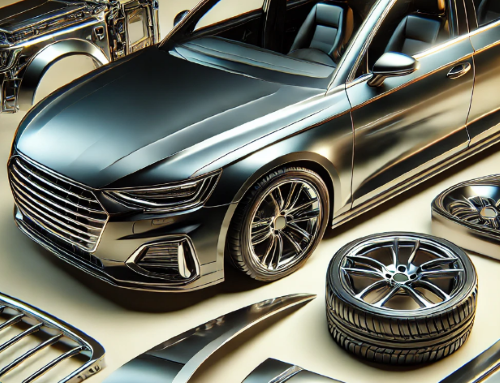
Introduction
Titanium, often called the “space age metal,” is a highly versatile material used in a variety of industries, including aerospace, medical, and automotive industries. In the automotive industry, titanium is prized for its strength, light weight, and corrosion resistance. This article introduces the common uses of Ti in automobile parts and how it enhances vehicle performance and durability.
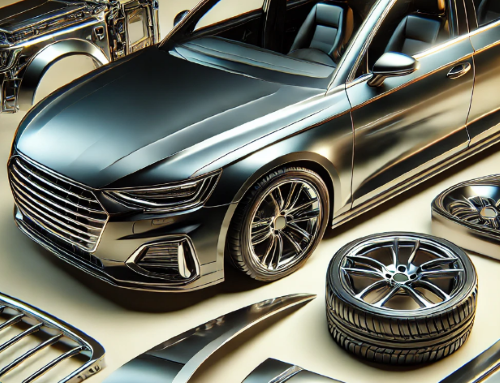
1. Engine Components
One of its primary applications in the automotive industry is in engine components. Titanium’s high strength-to-weight ratio makes it ideal for parts that undergo significant stress and heat, such as valves, valve springs, and connecting rods.
Ti valves, in particular, are used as performance engine components because they allow for higher engine speeds and more efficient operation.
Titanium connecting rods, which link the piston to the crankshaft, are commonly used in high-performance engines. These parts must withstand immense force and high temperatures. Titanium rods offer a combination of lightness and strength that steel cannot match, resulting in faster engine response and improved overall engine performance.
Further reading: Advantages and Disadvantages of Titanium Used in the Automobile Industry
2. Exhaust Systems
Titanium’s resistance to heat and corrosion makes it an excellent material for exhaust systems. Ti exhausts are popular in motorsports and high-performance vehicles, where reducing weight and maximizing durability are crucial. Titanium exhaust pipes are lighter than their stainless steel counterparts, which helps reduce the overall weight of the vehicle and improves handling.
Titanium is also more resistant to the heat generated by exhaust gases, meaning that titanium exhaust components can maintain their integrity over longer periods. This is particularly important in performance cars, where the exhaust system is subjected to high temperatures during intense driving conditions. Additionally, titanium’s corrosion resistance ensures that exhaust parts are less likely to rust, even when exposed to moisture, road salt, and other environmental elements.
3. Suspension Components
In performance vehicles, suspension components are crucial for ensuring a smooth and controlled ride. Titanium is increasingly used in shock absorbers, springs, and control arms due to its combination of strength, lightness, and fatigue resistance. By reducing the weight of suspension components, automakers can improve handling and responsiveness without sacrificing strength or safety.
Titanium suspension parts can be found in high-performance cars and motorsports vehicles where performance is paramount. The use of titanium in suspension systems helps maintain vehicle stability at high speeds while offering the necessary durability to withstand the forces exerted during sharp turns and jumps.
4. Wheels and Brake Components
Titanium is also used in the production of wheels and brake components. While titanium wheels are not yet common in everyday vehicles due to their high cost, they are becoming increasingly popular in racing and luxury automobiles. Titanium wheels offer a lighter alternative to traditional steel and aluminum wheels, improving acceleration, braking, and handling performance by reducing unsprung weight.
In the brake system, titanium is often used in brake calipers and rotors. Titanium brake calipers offer improved performance due to their light weight and ability to withstand high temperatures without deforming or corroding. Titanium rotors, though less common, are sometimes used in high-end performance cars because they offer exceptional strength and heat resistance.
5. Fasteners and Bolts
Titanium is used in a variety of fasteners and bolts throughout a vehicle. These small yet crucial components ensure that parts remain securely attached under extreme conditions. Titanium bolts and nuts are frequently used in high-performance engines, exhaust systems, and suspension components, where strength, resistance to corrosion, and weight reduction are important considerations.
Titanium fasteners are especially useful in racing vehicles and high-performance cars where every gram counts. The use of titanium bolts can help reduce the overall weight of a vehicle without compromising the integrity of the structure or safety.
6. Chassis and Structural Components
Titanium is also used in chassis and structural components of high-performance vehicles, particularly in motorsports. These parts must be extremely strong to withstand the forces of racing while being as lightweight as possible to maximize speed and handling. In motorsport, titanium is often used in frame components and roll cages, where weight reduction is crucial to performance.
Conclusion
Titanium’s unique properties make it an indispensable material in the automotive industry. Its strength, lightweight nature, and resistance to heat and corrosion allow for improved vehicle performance, durability, and aesthetics. While titanium’s high cost remains a limiting factor for widespread adoption, its use in key automotive components continues to grow as manufacturers seek to push the limits of speed, efficiency, and design.
As technology advances and manufacturing processes improve, titanium may become more prevalent in the mainstream automotive market. For more titanium products, please check Advanced Refractory Metals (ARM).