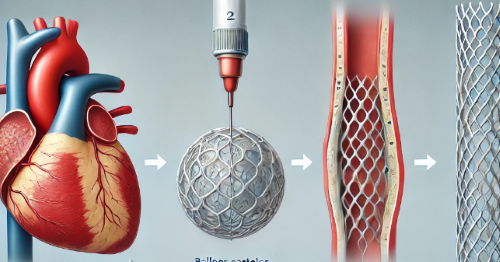
1. Challenges in Manufacturing Nitinol Vascular Stents
Nitinol, an alloy of nickel and titanium, is one of the most important materials used in the production of self-expanding vascular stents. Nitinol’s unique properties, such as superelasticity, shape memory, excellent biocompatibility, and corrosion resistance, make it an ideal material for cardiovascular implants.
However, Nitinol’s high strength, large plastic deformation, and severe work hardening make it difficult to process using traditional methods. Additionally, vascular stents are small, intricate devices that require extremely high precision in both geometry and surface smoothness.
Therefore, the manufacturing and polishing processes are crucial to ensuring that the stent can be safely implanted in the human body and function as intended.
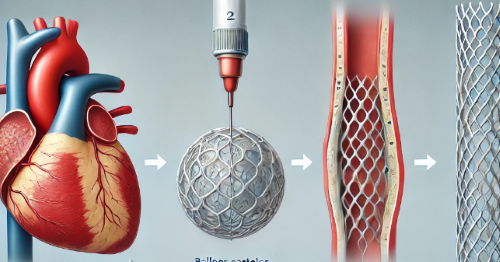
2. Manufacturing Process of Nitinol Vascular Stents
Nitinol vascular stents are typically manufactured through a series of steps:
- Laser cutting: The most common method used to shape Nitinol stents. Laser cutting offers high precision, non-contact processing, and the ability to create complex geometries.
- Surface treatments, including heat treatment, sandblasting, acid pickling, and electropolishing, are applied to improve nitinol vascular stent’s surface quality and mechanical properties.
- Final inspection: Ensuring that the stent meets strict medical standards for implantation.
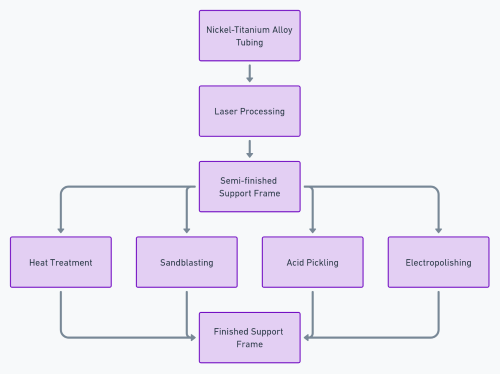
3. Polishing Processes for Nitinol Stents
Once the Nitinol stent is shaped, it undergoes several polishing processes to remove surface defects, enhance smoothness, and ensure the surface is clean and free from contaminants.
3.1 Heat Treatment and Its Effects
Heat treatment is used to refine the mechanical properties of Nitinol vascular stents. The heat treatment temperature and duration significantly affect the tensile strength and shape memory behavior of the material.
- At 400°C to 450°C, the mechanical properties of the Nitinol stent fluctuate with increasing heat treatment time. At higher temperatures, such as 500°C and 550°C, the tensile strength gradually decreases over time.
- Stress-strain analysis shows that heat-treated Nitinol at these temperatures maintains stable superelasticity, but prolonged heat treatment can cause excessive residual strain and negatively affect the stent’s performance. Proper control of the heat treatment parameters is crucial to maintaining the stent’s desired mechanical properties.
3.2 Sandblasting
Sandblasting is an important step in ensuring the smoothness of the stent’s surface. The process removes surface contaminants, such as oxides, burrs, and machining residues, improving the stent’s biocompatibility.
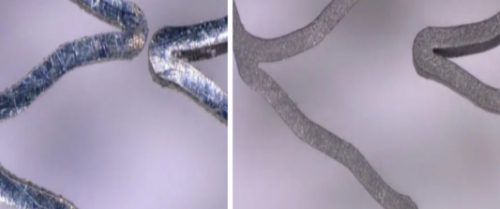
The stent’s surface condition before and after sandblasting
- Sandblasting with aluminum oxide followed by glass bead blasting helps achieve smooth edges and minimal material removal, particularly at the stent’s inner and outer diameters.
- Glass bead blasting ensures that the stent’s critical dimensions remain intact while improving surface smoothness and enhancing the stent’s fatigue life by preventing material loss.
3.3 Acid Pickling
After laser cutting, Nitinol vascular stents develop a black oxide layer and residual debris, which can cause complications if left untreated. Acid pickling is used to remove these unwanted surface layers.
- Hydrogen embrittlement is a risk during acid pickling, as prolonged exposure can degrade the material’s ductility. Thus, controlling the pickling time is essential to avoid reducing the mechanical performance of the stent.
- Studies show that excessive acid exposure (beyond 2 hours) can decrease the stent’s diameter, breaking strength, and bending fatigue resistance. Proper timing during acid pickling ensures the removal of surface oxides while maintaining material integrity.
3.4 Electropolishing
Electropolishing is one of the most effective methods for achieving a smooth, shiny surface on Nitinol vascular stents. This electrochemical process removes surface roughness and improves the overall performance of the stent when implanted.
- In acid-acid systems, sulfuric and phosphoric acids are typically used for electropolishing. These acids can quickly and effectively remove surface oxides and contaminants. However, controlling the polishing time is essential to avoid over-polishing, which can degrade the material.
- Acid-alcohol systems have been developed to improve the stability of the electropolishing process. The addition of alcohol increases viscosity, allowing for controlled material removal while preserving the stent’s surface properties.
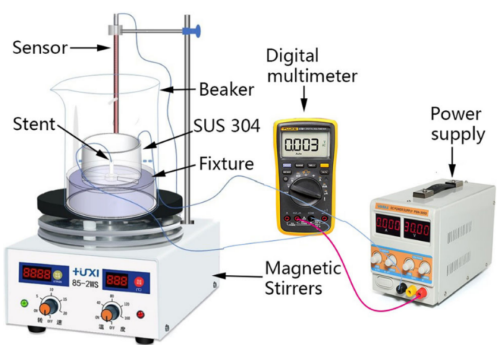
Conclusion
The polishing processes of Nitinol vascular stents are crucial for these life-saving medical devices. Each step of the process, from heat treatment and sandblasting to acid pickling and electropolishing, plays a role in refining the stent’s surface quality and mechanical properties.
These processes ensure Nitinol vascular stents meet strict geometric and mechanical standards for implantation, while providing long-term reliability and compatibility. Advanced Refractory Metals (ARM) supplies high-quality metal components for Medical, Surgical, and Dental equipment manufacturers. From Nitinol products to tantalum capillary tubes and marker bands, we offer stock and custom metal fabrication for medical equipment production. Please check our homepage for more information.
Reference:
[1] Daram P, Hiroto T, Watanabe M. Microstructure and Phase Evolution of Functionally Graded Multi-Materials of Ni–Ti Alloy Fabricated by Laser Powder Bed Fusion Process [J]. Journal of Materials Research and Technology, 2023, 23:5559.
[2] Lanying Wang, Wentao Cao, Heng Yang. The Adverse Effect of Pickling on the Mechanical Properties of Ni-Ti Alloys and its Elimination [J]. Metal Products, 1997, (04):11.
[3] Miao Zhang, Daihua He, Xinkuan Liu, et al. Progress in Electrolytic Polishing of Medical Nitinol Alloys [J]. Nonferrous Materials and Engineering, 2017, 38 (05):302.
[4] Shaozhen Zhu, Jie Wang. Constitutive Relations and Microstructure Evolution During Thermo-Mechanical Deformation of Medical Nitinol Alloys [J]. Iron Steel Vanadium Titanium, 2022, 43 (06):51.
[5] Y. Wang, X. Wei, Z. Li, et al. Experimental Investigation on the Effects of Different Electrolytic Polishing Solutions on Nitinol Cardiovascular Stents [J]. Journal of Materials Engineering and Performance, 2021, 30 (6):4318.
[6] Yanyan Wang, Jian Luo, Yong Li, et al. Effect of Heat Treatment on the Shape Recovery Ability of NiTi Self-Expanding Vascular Stents [J]. China Medical Devices Journal, 2021, 45 (02):119.
[7] Benli Wang. Research and Application Progress of Nitinol Shape Memory Alloys [J]. New Materials Industry, 2021, (04):28.
[8] Yongheng Zhou, Hongyun Liao, Songhao Liu. Laser Precision Cutting Technology for Vascular Stents [J]. Applied Laser, 2005, (03):161.