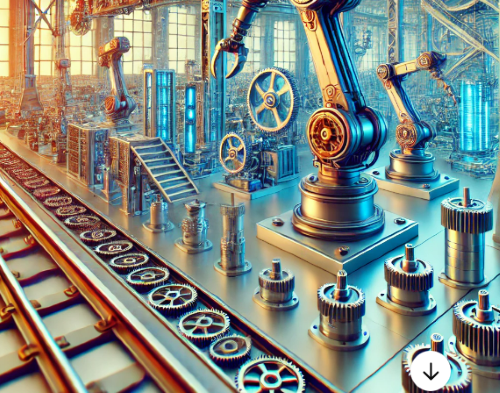
Introduction
Shape memory alloys (SMAs), particularly nickel-titanium alloys (Nitinol), are a unique class of materials that can recover their original shape after deformation when exposed to a certain temperature. This characteristic has led to their widespread use in various industries, particularly in the mechanical sector. In this article, we will explore the key applications of SMAs in the mechanical industry, highlighting their unique properties and the benefits they offer.
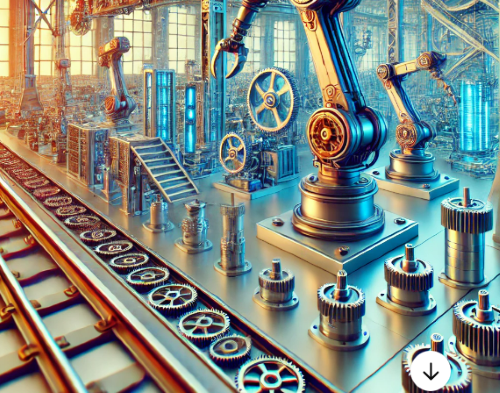
What are Shape Memory Alloys?
Shape memory alloys are metals that undergo a reversible transformation between two different crystal phases: martensite (low temperature) and austenite (high temperature). When the alloy is deformed in its martensitic phase and then heated, it reverts to its original shape, a process known as the “shape memory effect.” Some SMAs also exhibit “superelasticity,” meaning they can return to their original shape after significant strain without needing heat activation.
Related reading: Nitinol – Amazing Shape Memory Alloy
Shape Memory Alloys in the Mechanical Industry
1. Actuators and Control Systems
One of the most notable uses of SMAs in the mechanical industry is in actuators and control systems. Traditional actuators, such as motors and hydraulics, can be bulky and complex, but SMAs offer a simpler, more compact solution. SMAs can be used to create actuators that respond to temperature changes, causing precise mechanical movements. This is particularly useful in industries like aerospace and automotive, where lightweight, compact, and reliable components are essential.
Examples:
– Aerospace applications: SMAs are used in jet engines and space exploration equipment for adaptive control surfaces, such as flaps or panels that can change shape in response to temperature variations to optimize performance.
– Automotive systems: SMA-based actuators are employed in systems like automatic air vents, variable geometry turbochargers, and temperature-regulated mirrors.
2. Vibration Damping
SMAs possess excellent damping capabilities due to their ability to absorb mechanical vibrations. When subjected to stress, SMAs can dissipate energy through phase transformation, reducing the intensity of vibrations in mechanical systems. This makes them highly effective in applications where vibration control is crucial, such as in aerospace and heavy machinery.
Examples:
– Helicopters and airplanes: In aerospace, SMAs are used in rotor blades and structural components to dampen vibrations, improving stability and reducing noise.
– Bridges and buildings: In civil engineering, SMAs are applied to dampen vibrations in bridges and tall buildings, making structures more resistant to earthquakes and high winds.
3. Couplings and Fasteners
In mechanical systems, couplings and fasteners play an important role in connecting different components. SMAs, with their ability to change shape in response to temperature, offer innovative solutions for self-tightening or self-releasing couplings. These components can be pre-set to tighten or loosen when heated or cooled, allowing for adaptive and automatic assembly or disassembly.
Examples:
– Pipeline couplings: SMAs are used in oil and gas pipelines for couplings that can tighten when exposed to high temperatures, ensuring secure connections under fluctuating environmental conditions.
– Automotive fasteners: SMA fasteners are used in automotive assembly lines for quick and automated part assembly, reducing labor costs and improving manufacturing efficiency.
4. Temperature Control Systems
SMAs are highly sensitive to temperature changes, making them ideal for use in temperature control systems. They can be integrated into mechanical systems where automatic responses to temperature fluctuations are necessary. When the temperature crosses a specific threshold, the SMA element activates, opening or closing a valve, vent, or damper, depending on the requirement.
Examples:
– Fire safety systems: In fire safety, SMAs are used in automatic fire suppression systems. When exposed to high temperatures, the SMA actuators can activate sprinklers or fire doors without external power sources.
– Heating, Ventilation, and Air Conditioning (HVAC): SMAs are used in HVAC systems to automatically control airflow by adjusting vents or dampers based on temperature changes.
5. Adaptive Materials and Structures
SMAs enable the creation of adaptive materials and structures that can change their shape, stiffness, or mechanical properties in response to environmental conditions. This property is particularly beneficial in robotics and the automotive industry, where materials must adapt to changing loads, environments, or tasks.
Examples:
– Adaptive wings in aircraft: SMAs are used to create adaptive wings that can change their shape during flight, improving aerodynamics and fuel efficiency.
– Automotive suspension systems: SMAs are integrated into car suspension systems that can adjust stiffness based on road conditions, providing smoother rides and improved handling.
6. Microelectromechanical Systems (MEMS)
SMAs are also gaining traction in microelectromechanical systems (MEMS), where they are used to create miniature actuators and sensors. Their ability to perform precise movements in response to electrical or thermal stimuli makes them highly suitable for applications that require compact and efficient control mechanisms.
Examples:
– Medical devices: SMAs are used in MEMS-based medical devices for minimally invasive surgeries, where micro-sized actuators can precisely control surgical instruments or deploy stents inside the human body.
– Miniature robotics: In robotics, SMAs provide compact and powerful actuators for microbots used in surveillance, exploration, or even biological applications.
Advantages of SMAs in the Mechanical Industry
- Lightweight and Compact: SMAs are ideal for applications where size and weight are critical factors, such as in aerospace, automotive, and robotics. Their high power-to-weight ratio allows for efficient performance in small spaces.
- Reduced Complexity: Unlike traditional systems, which may require multiple components for motion control, SMAs can perform similar functions with fewer parts, reducing system complexity and increasing reliability.
- Energy Efficiency: SMAs can convert thermal energy directly into mechanical motion, reducing the need for external power sources in certain applications.
- Longer Lifespan: SMAs have excellent fatigue resistance and can undergo many cycles of shape recovery without degradation, making them durable and reliable in demanding applications.
Challenges and Future Directions
While SMAs offer many advantages, they are not without challenges. One of the primary limitations is their relatively slow response time in certain applications, as they rely on temperature changes to activate. In addition, controlling their precise activation can be difficult, especially in complex environments. Research is ongoing to improve the control mechanisms, speed, and efficiency of SMA-based systems.
In the future, advancements in material science and manufacturing techniques could lead to new types of SMAs with faster response times, greater durability, and expanded temperature ranges. These improvements will likely open new possibilities for SMAs in even more areas of the mechanical industry.
Conclusion
Shape memory alloys are revolutionizing the mechanical industry by providing smart, adaptive solutions for actuators, vibration control, temperature regulation, and much more. Their unique ability to recover shape and perform precise mechanical functions in response to environmental stimuli offers significant benefits in terms of simplicity, efficiency, and durability. As research continues to advance, the applications of SMAs are expected to expand, driving innovation across a wide range of industries. For more nitinol products, please check Advanced Refractory Metals (ARM).