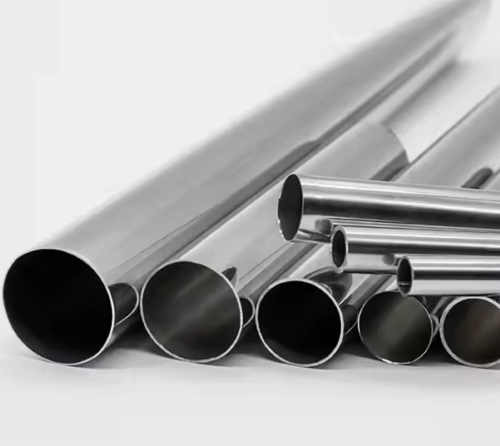
Introduction
In the world of materials science, titanium and stainless steel stand out for their unique properties and versatile applications. While both metals are integral to modern industry, they each offer distinct advantages and are suited to different purposes. This article explores the composition, strength, weight, corrosion resistance, thermal properties, machinability, workability, applications, cost, and biocompatibility of titanium and stainless steel.
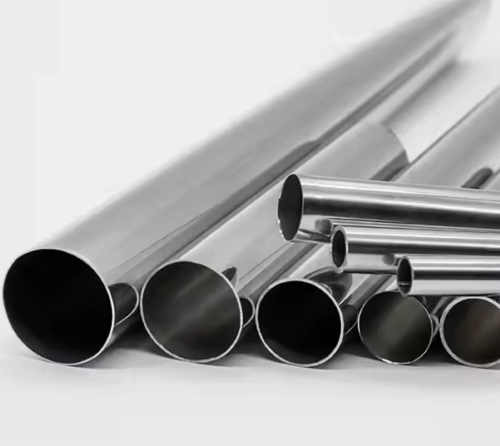
1. Composition and Structure
Titanium is primarily composed of the element titanium (Ti), often alloyed with aluminum and vanadium. Its hexagonal close-packed (hcp) crystal structure imparts high strength and low density. In contrast, stainless steel is an alloy of iron (Fe) containing at least 10.5% chromium (Cr) and often includes elements such as nickel (Ni), molybdenum (Mo), and carbon (C). Stainless steel typically has a face-centered cubic (fcc) crystal structure in its austenitic phase, but it can also be martensitic or ferritic depending on the specific alloy.
2. Strength and Weight
One of the standout features of titanium is its high strength-to-weight ratio. Depending on the grade and alloy, titanium’s tensile strength ranges from approximately 430 to 1400 MPa, while its density is about 4.5 g/cm³, roughly 60% that of steel. This makes titanium particularly advantageous in applications where weight reduction is critical, such as in aerospace and sports equipment.
Stainless steel, on the other hand, offers a wide range of strengths, typically between 200 and 800 MPa, depending on the alloy. Its density is around 7.8 g/cm³, making it heavier than titanium. While stainless steel may not match titanium in terms of weight savings, it compensates with versatility and cost-effectiveness.
3. Corrosion Resistance
Both titanium and stainless steel are renowned for their corrosion resistance, albeit in different environments. Titanium forms a stable, protective oxide layer that makes it exceptionally resistant to corrosion, even in harsh environments like seawater and industrial chemicals. This property is why titanium is extensively used in marine and chemical processing applications.
Stainless steel also boasts high corrosion resistance, especially alloys with higher chromium and nickel content. However, it can be susceptible to pitting and crevice corrosion in chloride-rich environments. Despite this, its general resistance to oxidation and staining makes stainless steel a popular choice for kitchen appliances, medical instruments, and architectural applications.
4. Thermal Properties
When it comes to thermal properties, titanium and stainless steel differ significantly. Titanium has a melting point of approximately 1,668°C (3,034°F) and a relatively low thermal conductivity of about 21.9 W/m·K. Its coefficient of thermal expansion is moderate at around 8.6 µm/m·K. These properties can limit titanium’s use in heat transfer applications but make it stable at high temperatures.
Stainless steel, with a melting point ranging from 1,375 to 1,530°C (2,507 to 2,786°F), offers higher thermal conductivity, typically between 15 and 25 W/m·K. However, its coefficient of thermal expansion is higher, around 16–17 µm/m·K, which must be considered in applications involving temperature fluctuations.
5. Machinability and Workability
Machinability and workability are crucial factors in material selection. Titanium is more challenging to machine due to its tendency to gall and its low thermal conductivity, which can lead to tool wear. However, it possesses good ductility and can be cold-formed, albeit requiring more force and special handling compared to steel.
Stainless steel generally offers easier machinability, especially in austenitic and ferritic grades. Its excellent ductility and formability allow for cold-forming and welding with relative ease, making it a preferred material for many industrial and consumer applications.
6. Applications
The unique properties of titanium and stainless steel dictate their applications. Titanium is widely used in aerospace for airframes and engine components, in medical devices and implants due to its biocompatibility, and in marine and chemical processing for its corrosion resistance.
Stainless steel’s versatility makes it ubiquitous in construction, automotive, medical, and food processing industries. It is commonly found in structural components, exhaust systems, surgical instruments, and storage tanks.
7. Cost
Cost is a significant consideration when choosing between titanium and stainless steel. Titanium is generally more expensive due to its extraction and processing costs, often being several times the price of stainless steel. This higher cost can be justified by its performance in specific high-demand applications.
Stainless steel, while varying in price depending on the alloy and market conditions, is generally more economical. Its cost-effectiveness, combined with its versatile properties, makes it a preferred choice for a wide range of applications.
8. Biocompatibility
In terms of biocompatibility, titanium is unmatched. Its inertness and compatibility with human tissues make it ideal for implants and medical devices. Stainless steel also offers good biocompatibility and is used in surgical instruments and some implants, though it can cause allergic reactions in some individuals.
Conclusion
In summary, both titanium and stainless steel have their distinct advantages and are suited to different applications. Titanium’s high strength-to-weight ratio, exceptional corrosion resistance, and biocompatibility make it ideal for aerospace, medical, and high-performance applications. Stainless steel’s versatility, cost-effectiveness, and good mechanical properties make it a staple in construction, automotive, medical, and food processing industries.
The choice between these two materials ultimately depends on the specific requirements of the application, including strength, weight, corrosion resistance, cost, and machinability. For more titanium products, please check Advanced Refractory Metals (ARM).